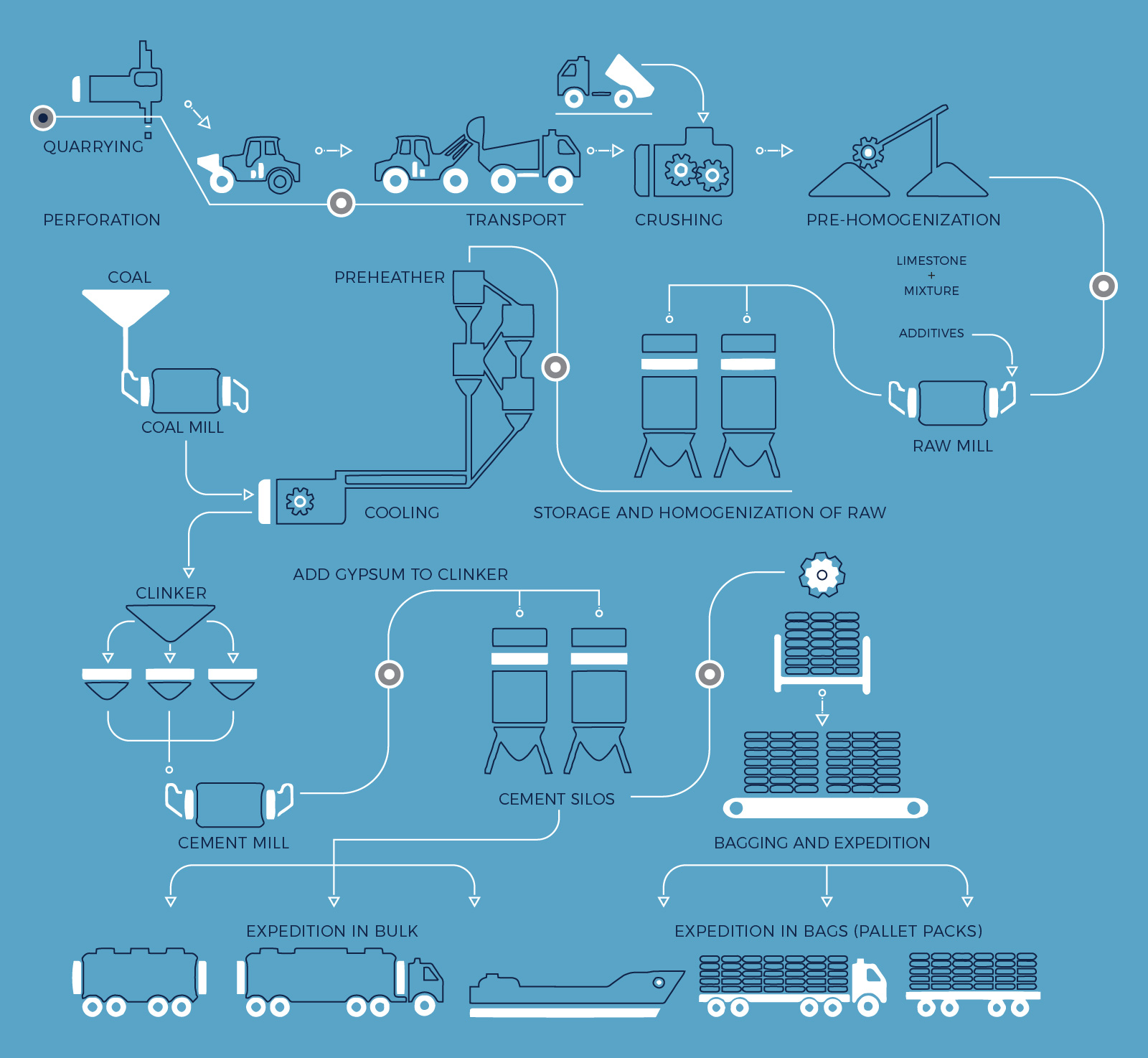
The raw materials consist of a carefully controlled mixture of limestone, marl and clay. Corrective substances such as sand and iron are sometimes added as well.
The materials are normally sourced from quarries and open cast mines. The work process is carried out on platforms, storeys, or else along vertical sections working at the entire height of the mineral deposit.
Through a computer-controlled process, the raw materials are selected and the right quantities are measured for the desired quality outcome of the clinker. Once the proportions of the raw materials have been defined, they are taken from their storage locations and transported to mills where the “raw mix” is produced consisting of a finely milled and carefully controlled blend of the raw materials.
This milling process commonly uses tubular grinders with two chambers containing metal balls of varying diameters, or else vertical mills. In either case, the raw materials have to be dried
For the sake of economy, the heat contained in the exhaust gas from the kilns is used in the drying process and for propelling the raw mix from the grinder to the storage silo.
Cement is then finally produced by finely milling the clinker, which is the main component, as well as gypsum and other additives (fly ash, slag, pzolane, lime filler, etc.).
The milling process may involve the use of vertical mills or else, more often, tubular mills with one, two or three chambers, operating in an open or closed circuit. When the circuit is closed, separators are used to reject the coarser grains, which return to the milling circuit. More recently, in order to save energy, roller press systems are used as pre grinders in some plants.
The materials are added in precise defined proportions, by keeping with the quality plan and relevant standards and specifications. The cement produced is usually transported by pneumatic or mechanical means and then stored in silos..
The quarried blocks measure up to one m3 and have to be crushed to the degree of fineness needed for the subsequent steps in the process.
A cement plant needs to be able to store large quantities of raw materials, to avoid production stoppages and to ensure that it operates continuously. The storage stage can also be combined with pre-homogenization.
The raw mix is then heated in kilns of which it’s type and size vary depending on the technology used by each manufacturer. They consist of a rotating tube, installed at an incline of between 2.5 and 5%, rotating between 1.5 and 2.5 r.p.m. and up to 85 m long. The tube is lined with heat resistant materials for protection and reduction of heat loss. In order to achieve clinkerization, a temperature of around 1450º C is required and is obtained by burning pulverized coal, petcoke, fuel oil, natural gas or other alternative fuels. The heating process starts as soon as the raw mix is taken from the storage silos and reaches the pre-heating system which occurs when it circulates against the current of the exhaust gases from burning the fuel. The rotating movements and the slope allow the material to be transported through the kiln.
When the clinker formation is complete, the cooling process starts. Initially it moves the clinker to the entrances of the coolers, and then into the coolers themselves. The most common type of coolers are the satellite and grate collers. To speed up the process, cooling air is blown in against the clinker flow, and the resulting hot air is used for burning the fuel.
The kiln is always complemented by a cooling system for the clinker based on the following reasons:
It is practically impossible to remove and transport clinker when it is still incandescent
Rapid cooling improves the quality of the clinker
Recovery of the heat carried by the clinker improves the thermal yield of the process
The clinker transporters, which have to withstand the temperature at the kiln exit approximately 200º C), carry it to the silos or horizontal silos.
A bagging machine packages the produced cement. Bags are then piled on pallets or else assembled in large plastified bundles. The cement which is dispatched in bulk, is transferred directly from the storage silos into the cement trucks or rail tankers.
The choice of packaging and means of distribution (road, rail or sea) is a critical decision in the competitive environment in which cement companies operate.